Rejuvenated 4 Charming Storefronts on Columbus Ave
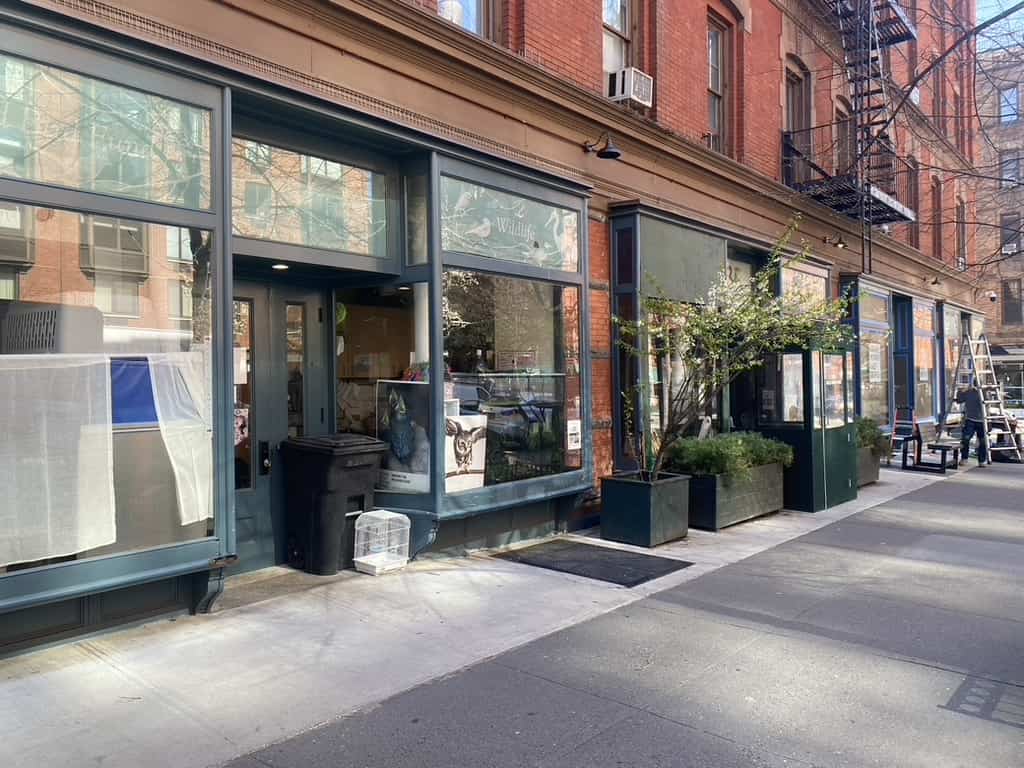
Service:
Repair
Products:
Custom
Address:
Columbus Avenue
New York, NY 10024
Highlights:
By the mid 1890s, Columbus Avenue had already developed its present architectural character, which primarily consisted of tenements, residential hotels, along with a few commercial buildings. And the time had come for the storefronts to be rejuvenated.
In the realm of building maintenance and restoration, meticulous attention to detail is paramount to ensure the longevity and visual appeal of such structures. The comprehensive scope of work detailed here involves a wide array of tasks, ranging from refurbishing joints, crafting intricate molding, and addressing rot issues to refinishing the exterior of storefront units. Each unit’s unique needs are elaborated upon, encompassing structural reinforcements, woodworking, and glass maintenance.
Here is a thorough exploration of the tasks for Units 1, 2, 3, and 4:
Unit 1: The primary focus for Unit 1 was on the revitalization of joints, a critical element for structural integrity. This entailed the painstaking process of the removal of existing material, which was then replaced with marine epoxy – a robust adhesive well-suited to withstand outdoor elements.
To preserve the unit’s original aesthetic, new custom made molding knives were fashioned. These knives were instrumental in replicating the precise profile of the existing molding, which ensured a seamless integration with the unit’s overall design.
Sections of the bullnose that had succumbed to rot were expertly removed, and where necessary, the entire bullnose was replaced. To fortify this architectural element against moisture, the new molding was meticulously crafted from Mahogany, with the addition of a protective drip detail on the underside.
The process of resetting the bullnose involved employing marine epoxy and specialized types of glues, ensuring a secure and resilient bond that will endure the rigors of outdoor exposure. Furthermore, replacing the molding on the underside serves a dual purpose, enhancing joint sealing and safeguarding the unit’s rejuvenated visual appeal.
If the under sheeting had been compromised due to rot, it was either re-secured or replaced, contingent on the extent of the damage. This step is pivotal in maintaining the structural integrity of the unit.
An existing louver above the door was flipped, in order to optimize its functionality and aesthetics.
Finally, the exterior of the storefront was be meticulously prepared and painted. This step was essential for both the unit’s appearance and its protection against the elements.
Unit 2: The focus for Unit 2 was exclusively on exterior restoration. The preparatory work involves extensive surface preparation and painting, in order to rejuvenate and protect the unit’s exterior. The objective here was to maintain the unit’s visual appeal and safeguard it against the effects of weather and other environmental elements. The interior, however, was not included in this restoration scope.
Unit 3: Similar to Unit 1, the crux of Unit 3’s requirements revolved around the meticulous restoration of joints. Existing material was removed, and marine epoxy was applied to fortify the joints against outdoor conditions.
In this unit, more significant alterations were needed. New stiles and rails were crafted for the left side of the front. These components were pivotal for maintaining the structural integrity and appearance of the unit. Their installation, combined with marine epoxy and glue for bullnose reattachment, enhanced the unit’s stability.
Just as in Unit 1, the molding on the underside will be replaced to improve joint sealing. Under sheeting will also be re-secured or replaced if compromised by rot, a necessary step to maintain structural integrity.
Similar to Unit 1, an existing louver above the door will be flipped, presumably to ensure optimal functionality and aesthetics.
The exterior of the storefront underwent preparation for painting, which preserved the unit’s aesthetic appeal and safeguarded it from harsh environmental elements.
Unit 4: This unit mirrored the approach taken in Unit 1. Joint restoration was at the forefront, with meticulous removal of existing material and the application of marine epoxy, ensuring structural integrity and durability.
Rotten sections of the bullnose were removed as needed, and new Mahogany molding with a drip detail was fabricated. The bullnose was reset using marine epoxy and exterior grade glue to secure it effectively.
Molding on the underside was replaced, serving as both an aesthetic enhancement and an improved joint seal.
The unit’s exterior was thoroughly prepared and painted, providing protection and enhancing its visual appeal.
Additionally, a LPC (Landmarks Preservation Commission) permit, ensuring compliance with preservation regulations.
Lastly, there is a task separate from the main scope of work, which involved the de-glazing of an oversized pane of glass. The process entailed careful removal of the glass, cleaning the rebate, and re-fitting with high-performance glazing tape and silicone. The glass stop moldings were also refitted or replaced, ensuring glass security and longevity.
Furthermore, the installation of a new door weather strip was contributed to improved weather resistance and energy efficiency.
The tasks outlined for Units 1, 2, 3, and 4 represent a cohesive blend of expert craftsmanship, the use of specialized materials, and a laser focus on both structural integrity as well as aesthetic appeal. These efforts collectively ensured that the rejuvenated storefront units remained both visually appealing and resilient against the elements, while adhering to preservation regulations and enhancing energy efficiency.